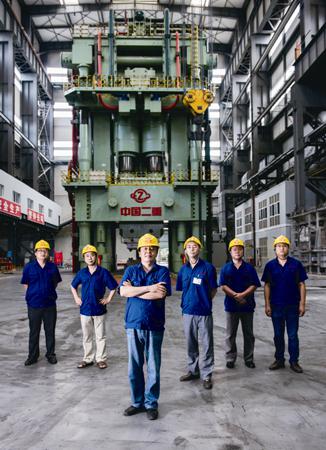
二重集团副总工程师陈晓慈(左三)与几十位工程师建造了世界最大的8万吨模锻压机。
大家都知道,机床工业被称为“工业之母”,通俗含意就是能制造机器的机器,这是一个国家工业实力的集中体现,但对于我们来讲这是一个弱项。
国产大飞机为什么建国六十多年了,刚刚造出来呀?首先就是发动机不过关,现在C911上的发动机也还是进口的。飞机发动机核心部件之一的涡轮盘是用高温镍基合金制造的,它要承受高温、高压和高速旋转的恶劣工况,需要的材料即要坚韧又要耐高温,制造它最大的难题,就是要用巨大的压力进行锻造,但制造出具有这种性能的母机对我们来说,很难。现在中国二重制造的8万吨模锻压机问世了,这意味着制造飞机发动机其中的一个瓶颈问题有望解决了。
2011年,济南二机床集团为福特汽车美国三家工厂定制了5条大型冲压生产线,每条线由多连杆压力机组成,总重6100吨,由双臂送料系统、拆垛机、清洗机、涂油机等设备组成,效率是普通生产线的3倍。
象这样的机床母机一个国家通常只有一台,有时可能全世界只有一台,算是制造业的镇国之宝了。可以说,在某些领域我们取得了一些成绩,这是我们机床工业之所得。
但不容乐观的是类似的荣誉并不是遍地开花的,我们可以夸耀的并不多。尽管改革开放三十多年来,取得的成绩也并不小,我国机床工业从一开始引进大量国外先进技术,合作生产各类数控机床,到后来甚至仿造出了五轴联动控制加工中心,但高精产品的核心关键技术是仿制不出来的,我们在人才、科研和自主创新上都乏善可陈。
比较以下这组数据,最能说明问题:
我国在改革开放之初的1980年,机床拥有量为283万台,其中粗加工车床构成比为43%,精加工机床占10%, 经过30年的发展,到2008年,中国机床工业约有5382家企业,机床拥有量约700万台,(美国约240万台、日本约140万台),粗加工机床仍占40%以上,精加工机床反而少于10%,这与国外由高效自动化机床和数控机床组成的精加工机床占比20%~30%相比,我国精加工机床构成比未增反降,突显出中国机床工业仍然十分落后。
建国60多年了,凝聚了我们三代人的青春,看看世界机床工业都发生了哪些巨变吧:不到60年里,美国机床工业超越了当时的世界霸主大英帝国,德国机床工业又在不到60年的时间里超过了美国,而小日本则在不到60年的时间里,跻身世界前三强。我们是不是有些汗颜?
回头看看我们走过的路,改革开放前耽误的三十年就不用说了,后三十年取得的成绩确实是有目共睹的,但问题也不少。尽管机床行业有政府制定的发展规划,可内容脱离实际,流于空泛,如2006年国家发改委制定的《数控机床发展专项规划》,要求至2010年,数控系统自主知识产权的要占数控机床总量的75%,功能部件配套自给率60%以上,国产数控机床要占领国内市场的50%以上等等,实在有些虚无飘渺。纵观近三十年行业政策史,失误很多,如无视国内机床行业的实际情况,规划只是停留在书面上,根本无法落实,缺乏的严谨科学的态度,对市场需求没有准确的分析统计,背离了行业发展规律。
除政策失误外,行业还存在两大问题:
一、不注重人才培养和自主研发,长期仿造国外,缺乏核心技术。
三十年成绩不可否认,但长期停滞在“引进、消化、吸收”的陈旧观念里,不思进取,一味仿造,造成机床行业在产业链的最低端长期徘徊,难以走出。加上忽视职业技术教育以及对企业技术人才的培养,行业人才供求失衡,流失严重,另外在改制过程中,许多有研发实力的科研院所被转制为企业,导致科研能力大大削弱,众多技术瓶颈难以突破,高精尖机床及核心零部件大量依赖进口,技术追赶成为空谈。
二、行业发展严重失调,各门类缺乏统一规划与配合。主要表现在主机与数控系统、功能附件、刀具之间的发展不相适应,脱节现象比较重要。
在近三十多年发展中,我国机床行业的产业结构主要以生产低中档产品为主,而发展最为迅速的数控机床,在核心技术和关键零部件上一直依赖进口,阻碍了技术创新和产业进步。国内机床产品普遍存在质量问题,稳定性、可靠性和一致性都比较差。主要原因是人心浮躁,急功近利,没人愿意潜心搞研究,都一味追求短期效益,技术工人普遍缺乏,后劲不足。
历数六十年发展的得与失,我们必须保持清醒,认识到问题的严重性,盲目乐观并不可取。我们之所以成为世界机床大国,主要是由于我们体量大,市场广阔,但让中国制造从大变强,却是一个艰巨的系统工程,需要政府提高对作为工业之母的机床工业的重视程度,并担当起强有力的组织者和策划者,调动各种有利资源,统筹安排,协调发展。随着智能制造和绿色制造的兴起,我们要抓住历史机遇,遵循市场规律,总结以往的经验教训,尽快在人才培育和技术创新上有所作用,把机床产业向高中端推进。