目前镜面电火花加工技术在精密型腔模具制造中逐步得以推广。本文就企业中镜面电火花加工应用的关键环节,结合实践分析了影响镜面加工性能的因素。通过控制各个工艺环节,可有效实现高质量、高效率的镜面电火花加工。对模具制造企业吸收与消化当前先进的电火花加工工艺具有实际的应用价值。
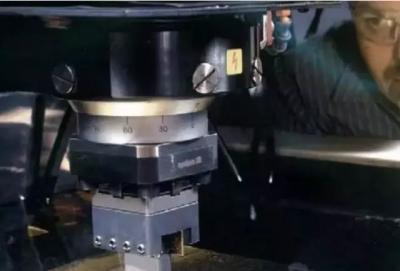
当前,模具制造技术的快速发展,赋予了电火花加工更高的要求。表面粗糙度是电火花加工的一项重要技术指标。目前通过对机床的改进和开发新的工艺方法,已能实现镜面电火花加工。所谓镜面电火花加工一般是指加工表面粗糙度Ra<0.2μm的电火花加工,同时加工表面具有镜面反光效果。该技术主要应用于精密模具的复杂型面的加工,电火花加工获得的高光洁度表面无需再进行手工抛光,避免了手工抛光导致的形状与尺寸精度缺陷问题,具有实际意义。
以下根据实践加工经验对镜面电火花加工应用的关键技术进行探讨。
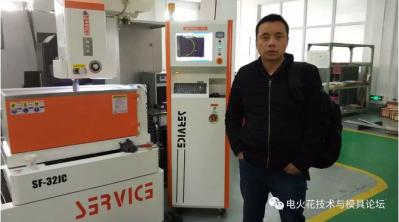
由于工件材料的化学成分和组织结构的不同,在相同的加工条件下,会产生不同的加工效果。有一些材料能获得良好的镜面效果,而一些材料却得不到镜面效果,甚至表面有条纹等异常情况。表1列出了多种常见工件材料的电火花镜面加工性能。需要注意的是,并不是电火花加工镜面效果不好的材料就说明其不属于镜面材料,如S136 ESR钢材本身具有出色的抛光性能,但使用电火花加工的镜面效果却不理想,这是因为电火花加工与抛光是两种加工原理完全不同的工艺方法。电火花加工的表面是由许多互相重叠的盘状凹坑组成,这些微小凹坑在光的反射下形成了闪光的镜面,不同材料电火花加工后所产生的微观凹坑形貌不相同,因此表面的光亮性也不相同。
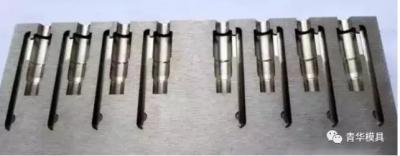
表1 常见工件材料的电火花镜面加工性能
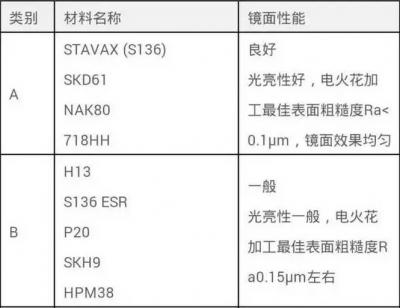
可以认为下列情况是工件材料影响镜面加工效果的一些原因:
(1)、含有大粒径的粗生碳化物或粗大晶体颗粒添加物对加工镜面不利,产生显微裂纹;
(2)、含硅成分有利于获得较好的镜面效果;
(3)、含有快削成分的硫S对加工镜面不利,易产生表面条纹;
(4)、材料轧制方向等胚料制造工艺因素对加工镜面不利,产生表面条纹;
(5)、金属夹杂物、气泡、氧化物等因素形成针眼和孔洞。
通常来讲,大多数塑胶模具钢能满足镜面电火花加工的要求,而大多数冷作模具钢则不能满足。
当材料的性能满足镜面电火花加工性能时,其硬度越高,电火花加工镜面的效果要好,如表2所示。一般要求镜面电火花加工的钢料应热处理淬硬至HRC>50。
表2 材料硬度对镜面效果的影响对比
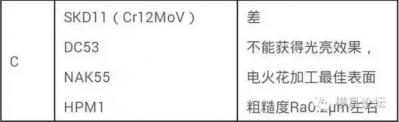
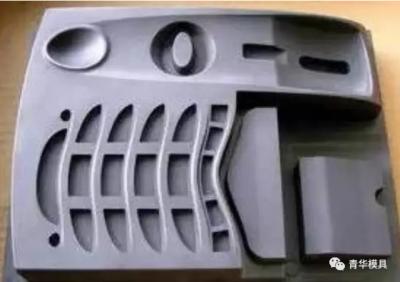
电火花加工的镜面效果与加工面积、形状、深度有直接的关系。
由于电火花加工的表面粗糙度主要取决于单个脉冲能量,通过降低单个脉冲的火花放电能量可产生表面粗糙度值低的反光表面,但这时的镜面加工仅限于小面积加工。随着加工面积的增大,电极和工件之间的寄生电容相应增大,当单个小能量放电脉冲作用于两极之间时,并不能引起两极间的火花放电,此时的间隙电压升高很慢,脉冲能量被储存于寄生电容中,只有当多个放电脉冲到来,寄生电容中储存了足够多的能量后,间隙电压逐渐升高到击穿电压,才引起火花放电,但此时的放电能量相当于多个放电脉冲能量的叠加,产生的放电蚀坑深度将大大增加,表面粗糙度值变大,加工表面便失去镜面效果。
为了实现大面积的镜面电火花加工,通过在工作液中添加一定数量的粉末,会显著地改善电火花加工后的表面粗糙度,达到类似镜面的效果,并能获得更快的加工速度(使精加工时间缩短20%-30%)。
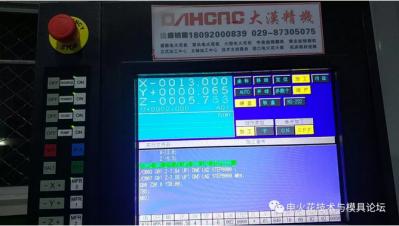
在不使用混粉加工工艺的情况下,加工面积越大越难以获得好的镜面效果。事实上,由于平动工艺的应用,电极并不是整个面积都接触,这种局部放电减少了“电容效应”,另外由于电极与工件之间在放电过程中本身也会产生一层均匀的炭黑层,其作用类似于混粉加工的意义,因此更大一些的加工面积(如1600mm2)通过优化工艺参数也能实现均匀一致的镜面效果。对于使用混粉加工工艺的情况,则可以轻松实现大面积(如10000mm2)的镜面效果。
从加工形状来看,简易形状比复杂形状要容易获得镜面。最容易获得镜面效果的形状是圆形,其次是方形、轮廓复杂的形状,难度最大的是多个型腔整体放电的类型。复杂形状的拐角、弧面处的镜面效果较容易出现不均匀、波纹等异常。
判断型腔镜面加工的难易程度还可以参考放电产生的炭黑层能否均匀覆盖于电极与工件表面的情况。例如底面比侧面更容易获得好的镜面效果,这是因为在整个放电过程中,底面始终处于被修整的状态,炭黑层能均匀分布在加工表面,但侧面是依靠平动加工来完成,炭黑层相对底面不能有效地覆盖。另外,深度越大的型腔,由于加工部位不能均匀地覆盖炭黑层,因此镜面效果的均匀性会受到影响。
电火花加工工艺数据库的配置内容主要包括电规准和预留量。一套镜面电火花加工数据库由多达十几个电规准组成。从粗加工电规准到精加工电规准,需要合理过渡电规准来逐步降低表面粗糙度。每一档电规准都应能够稳定放电,不产生拉弧、积碳等不良表面情况。同时每两档电规准之间需要预留合理的余量,后一电规准要能将前一电规准产生的放电凹坑修光。只有完美地将电规准和预留量搭配好构建一套加工数据库,才能在实际生产中实现镜面加工。
电规准包括电流、脉冲宽度、脉冲间隙、极性、电压及抬刀控制等参数。粗加工阶段的电规准使用较大的峰值电流与脉冲宽度,较小的脉冲间隙,使用正极性(电极为正)来实现高效率、低损耗加工,抬刀速度要快,有助排屑。中加工阶段电规准的电流依次减少,为了降低表面粗糙度值并实现稳定的放电加工,脉冲宽度大幅度减少,由于粗加工阶段已经将大部分加工量去除,中加工阶段的相对损耗并不大。精加工阶段通常在VDI18级(Ra0.8um)规准以下使用负极性加工(电极为负极),使用更小的脉冲宽度,通过电容储能来放电,这样实现了在精加工阶段也能保持较高的效率与放电稳定性。为了避免表面黑斑等缺陷,精加工阶段的电规准使用大脉间,以实现均匀一致的亚光精加工表面。
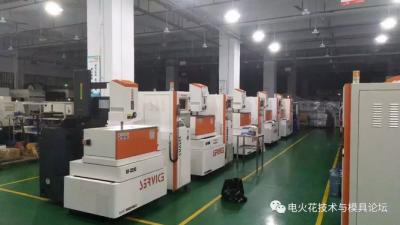
在精加工表面达到VDI12级(Ra0.4μm)左右时,就可以切换进入镜面加工。镜面加工的效果取决于最后这一档电规准的配置。从理论上来讲,镜面电火花加工电规准配置应选用小的峰值电流、小的脉冲宽度、较大的脉冲间隙;峰值电流选的越小,脉冲宽度越小,脉冲间隙越大,加工表面粗糙度值就越小。事实上,采用这种参数搭配方法,加工效率极低,太小的脉冲能量由于不能稳定放电导致不能获得均匀一致的镜面效果。实际的镜面加工,宜选用较大的峰值电流和较小的脉冲宽度,较大的峰值电流使得小脉宽条件下的放电击穿变得容易。镜面电火花加工采用负极性加工(电极为负),不能搭配电容。另外,抬刀控制参数的选择同样非常重要,与常规加工的选择也存在一些差别,如放电时间要设长些,抬刀高度不要太高,抬刀速度不能太快,这样设置的目的是为了使电极与工件之间能形成一层均匀的炭黑层,以维持稳定的电蚀过程,过勤的抬刀动作会干扰炭黑层的形成。

电规准之间的预留量会影响加工速度与表面粗糙度。较小的预留量加工效率高,但会导致表面修不光。最理想的加工状况是第一个条件加工完后,其后的加工只是修光第一个加工条件形成的表面不平度,而不打掉新的材料。但实际加工时,考虑到放电状况受到的制约因素千变万化,因此要考虑安全的预留量。VDI18以上的电规准的加工效率主要取决于各档规准之间的预留量,VDI18及以下的电规准,由于电蚀能力较弱,基本只起修光作用,如果严格地按照指定的尺寸执行加工,加工需要花费的时间就有可能很长。而实际上只要加工到要求的表面粗糙度后就可结束加工,因此数控电火花加工机床针对精加工规准通过定时加工功能来有效控制加工效率,也就是为每一档电规准设定修光时间。
先进的数控电火花加工机床的电规准的配置方法是智能化的,可以通过专家系统来自动生成加工工艺数据。编程时选择材料对、应用类型、表面粗糙度值,输入加工面积、加工深度、电极尺寸缩放量等,机床就能配置出加工电规准。
表3 某先进机床镜面加工工艺数据表(部分)
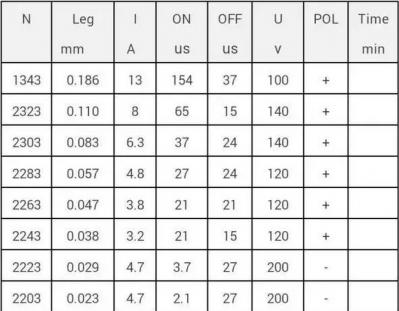
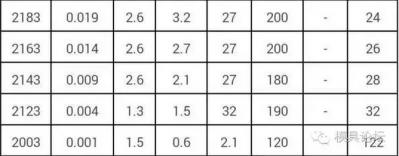
数控电火花加工机床的平动功能,电极沿着目标加工形状不断在摇动中加工,消除了电极的停滞,可实现型腔底面与侧面均匀一致的表面效果。在不使用平动工艺的加工中,即使是直径10mm的小面积也难以实现均匀一致的高光洁度镜面效果。平动工艺的应用避免了电极整个面积的集中接触放电,通过周期性的局部放电可实现较大面积的镜面加工。
镜面电火花加工需要选择合适的平动方式。大部分型腔的镜面电火花加工,加工过程中每一规准的平动量能随深度同时变化,也就是深度逐步加大,平动量也随之加大,底面与侧面处于同步加工的三轴联动方式。这种平动方式在小能量的精加工中,显著地提高了加工的稳定性,由于底面与侧面是同时进行加工,可有效启用定时加工功能,在指定的加工时间内实现侧面与底面的表面均匀一致的效果。
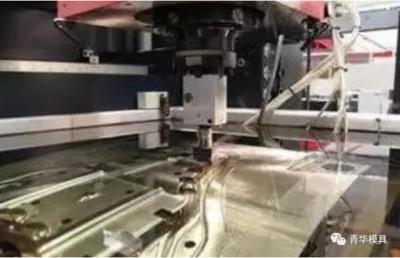
镜面电火花加工采用多电极更换的工艺方法。需要根据加工部位加工量的大小来确定使用几个电极进行加工。通常使用粗、精加工两个电极,粗加工电极尺寸缩放量取单边0.25mm,精加工电极尺寸缩放量取单边0.15mm,加工面积小或者仿形精度要求高时可取小一些。粗加工电极采用较大放电能量的电规准快速蚀除大量金属,表面达到VDI28(Ra2.5μm)即可,通常预留0.07mm左右的余量;精加工电极逐步修细,最终进行镜面加工。如果型腔已进行过预铣加工,加工量不大的情况,使用一个电极即可完成从粗到精的镜面电火花加工。
粗、精加工要求电极的一致性要好、制造精度要高,更换电极的重复装夹、定位精度要高。可以采用高速铣制造电极、使用基准球测量的定位方法、使用3R快速装夹定位系统进行重复定位等工艺来满足高要求。
镜面电火花加工要求使用纯度较高的紫铜作为电极材料(如日本三宝红铜),其加工性能良好,不易发生电弧放电,能获得均匀一致的加工表面。如果使用的紫铜电极材料的纯度不够会导致加工的镜面不均匀、局部缺陷等不良现象。
镜面加工用的电极必须进行精修抛光(至少要经过1000#砂纸的精抛),以达到表面粗糙度低值的表面。如果电极表面存在波纹、缺陷,并不影响加工表面目视的光亮效果,但测量其表面粗糙值会偏大于Ra0.2μm。镜面电火花平动加工中电极相对XY平面内作微小周期性运动能使电极表面的微观缺陷得到有效均化,有利于降低加工表面粗糙度值。根据加工经验,电极的表面粗糙度为Ra0.25μm的情况下同样能实现Ra0.1μm的镜面加工效果。
电火花工作液在加工过程中起着消电离、冷却、排除电蚀产物的作用。工作液应根据电火花加工的要求来进行选择,主要参考“粘度”指标,抗氧化性能和热稳定性也很关键,决定油品的使用寿命。低粘度有利于加工间隙中工作液的流动,将蚀除产物及加工产生的热量带走,使加工间隙及时恢复正常状态。镜面电火花加工使用的工作液粘性推荐为2~3 mm2/s,建议配用电火花油TOTAL EDM 22(运动粘度(40℃)2.4mm2/s;闪点102℃)。
混粉电火花加工在工作液中加入了一定数量的粉末颗粒,据国内外众多混粉加工的技术报道基本有硅粉、铝粉、镁粉、石墨粉几种。FORM20机床使用的粉末为GF加工方案公司研究的专用混粉溶液,其成分主要为石墨颗粒,大致长度小于8um,粉末添加的浓度要求为2g/L。每一次更换混粉液前需要过滤、清洁火花油,将加工过程中的残屑与失效的粉末过滤掉再加入混粉溶液,保证加工效果的使用时间在 350 ~400 小时。混粉液的浓度不够时,在较短的时间内不能达到表面有光泽的效果,当混粉浓度过大时,型腔的锐边棱角会被破坏,电极与工件之间较多粉末的存在会导致流动短路,严重时会在工件表面产生伤痕。
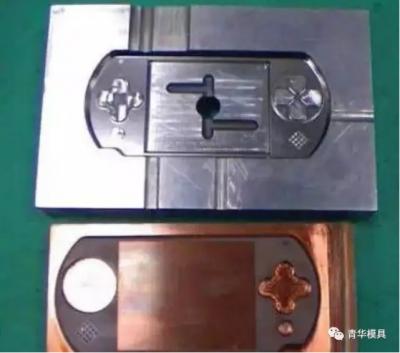
数控电火花加工一般在浸油加工的基础上加适当压力的侧冲液,以帮助有效排屑来提高加工效率。而镜面电火花加工过程中不能使用侧冲液,将工作液设置为轻微循环状态即可。侧冲液的冲刷作用力会破坏电极与工件之间的炭黑层,影响镜面加工效果的均匀性。
镜面电火花加工过程中,往往能保持高稳定的放电状态,一般不会产生积碳现象,因此在加工过程中应尽量不停机,尤其是不要将工件加工表面的粉末层清理掉,否则会严重影响镜面加工过程的持续进行。
加工完成后发现镜面效果不理想时,不要将工件拆下,使用镜面电规准再进行精修。精修时会发现放电状态非常不稳定,电极迟迟不能进入整体放电状态。在这种情况下,先使用气枪将电极与工件表面上的炭黑层完全吹干净,然后启动放电,并将电压值增大至200V~250V,电压加大后放电击穿变得容易,在短短的几分钟内可以观察到放电状态由局部放电转入到整体放电,这时再将电压值恢复至正常值。这个过程中电极与工件之间会重新产生炭黑层,需要待整个加工部位都出现均匀的炭黑层才能结束加工。
综上所述,通过选择合适的工件材料、高纯度的紫铜电极材料、低粘度的工作液,使用合适的平动工艺,同时合理配置工艺数据库,正确地处理加工过程,把握好这些关键的应用环节,就可以有效实现高质量、高效率的镜面电火花加工,对提升模具制造企业的工艺水平具有重要指导意义。
来源:青华模具